TON
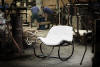
Továrně ohýbaného nábytku v
Bystřici pod Hostýnem neřeknou místní obyvatelé jinak než tonetovka. Výrobě
židlí a stolů se zde věnují již od roku 1861.
Výroba nábytku
– S ohýbáním překližkových dýh začal experimentovat zakladatel bystřické továrny
Michael Thonet již ve třicátých letech devatenáctého století. Ohýbaný nábytek
představil o několik let později, a to v roce 1841 na průmyslové výstavě v Koblenci.
„Zde došlo k osudovému setkání
s rakouským kancléřem Metternichem, který jej pověřil vybavením vídeňských
paláců,“ uvedl vedoucí řízení jakosti firmy TON Radmil Tomčík, který se zajímá o
historii společnosti a ohýbaného nábytku. V roce 1842 se Thonet přestěhoval
z rodného Boppardu do Vídně, kde vyvíjel vlastní modely židlí.
„Výrobní prostory ve Vídni po
několika letech nevyhovovaly jak velikostí, tak i dostupností potřebného
materiálu. V roce 1856 se rozhodl založit novou továrnu. Snadný přístup k
surovinám a dostatek pracovní síly zavedl Thoneta do moravských Koryčan. Výroba
v tomto závodu začala v roce 1857. Díky rostoucímu zájmu o ohýbaný nábytek byly
založeny další dvě továrny, a to v Bystřici pod Hostýnem (1861) a ve Vsetíně.
Továrna v Bystřici patřila k největším a nábytek se v ní vyrábí dodnes,“
uzavírá Tomčík.
Ivana Kocourková z oddělení marketingu zahájila prohlídku v
reprezentativních prostorách vily Thonet. Toto místo, kde dříve žila rodina
Thonetů, dnes slouží k prezentaci firmy a výrobků. Vyzkoušet si zde můžete
nejen současné modely židlí, ale i nahlédnout do historie podniku.
Nedaleko vily Thonet jsou dvě výrobní haly. „Dnes nábytek
vyrábíme v té mladší. Původní továrna postavená před 150 lety je již využívána
pouze v omezené míře, zejména pro přípravu a uskladnění materiálu,“ říká
na úvod Kocourková.
Přízemí slouží k přípravě řeziva, a to jeho základnímu
opracování, případnému změkčení, sušení a dalšímu požadovanému opracování.
Jednotlivé díly jsou předány do meziskladu, ze kterého putují do prvního
patra. Zde se montují připravené díly, je provedena povrchová úprava a ověřena
požadovaná kvalita hotového výrobku. Na závěr je zboží zabaleno a připraveno
k expedici.
Vraťme se ale zpět na úplný začátek výroby. Prvním krokem je
příjem materiálu. „Základem každé židle je dřevo, a to bukové. Výjimečně
je používán i jasan. Do areálu však nemíří celé kmeny či fošny, ale již hotové
hranolky. Dodavatel řeziva na základě objednávky připraví daný typ hranolků.
Ve výrobě používáme až 300 různých rozměrů. V minulosti jsme měli vlastní
hranolkárnu, ale ta již byla zrušena,“ uvedl vrchní mistr přípravy a
ohýbárny Pavel Hlava.
Z venkovních skladů řeziva jsou dodané hranolky převezeny do
výrobní haly. V tzv. přípravně je provedeno základní opracování. K úpravě
hranatých dílů je používána dvoustranná a čtyřstranná fréza. K vytvoření
kulatých profilů slouží tzv. protahovačka. Hranolky jsou dodávány v hrubé
míře, proto je nutné jednotlivé díly zapravit na přesné rozměry.
Doménou bystřické továrny je ohýbání dřeva. Před vlastním
ohybem je nutné dřevo změkčit, a to napařením v syté páře. K tomu slouží
pařicí kádě, ve kterých je dřevo vystaveno teplotě 100 stupňů Celsia a tlaku
dvou atmosfér. „Doba paření dřeva se odvíjí od náročnosti ohybu a průřezu.
Jeden centimetr materiálu vyžaduje přibližně hodinové paření. Čím silnější je
materiál, tím déle je třeba materiál napařovat,“ dodává Hlava.
Pro méně náročné ohyby slouží moderní vysokofrekvenční lisy. Ke
složitějším ohybům jsou využívány tvarovací stroje. Ohýbané dřevo je upevněno
do speciální formy s ocelovou pásnicí, na kterou se přenáší tahové pnutí při
ohybu – díky ní nedojde k prasknutí materiálu. Ohnutý díl je i s formou uložen
do košíku, který míří do sušící komory. Zde dosáhne dřevěný díl za jeden až
dva dny požadované vlhkosti. Po vysušení je díl vyjmut z formy a předán
k dalšímu zpracování.
K ohýbání dílů ve více rovinách nelze použít stroje, proto musí
být některé díly ohýbány ručně. Dva dělníci upevní dřevo do formy a následně
jej vlastní silou vytvarují do požadovaného tvaru. Při pohledu na dělníky
nikdo nepochybuje, že jde o fyzicky náročnou práci. Podle Pavla Hlavy naplní
jedna dvojice „ohybačů“ za směnu přibližně osm až deset košů. Každý z nich
pojme třicet dílů.
V další dílně jsou jednotlivé díly strojně opracovány –
například jsou do dřeva vyříznuty drážky, zabroušeny nežádoucí hrany a
zapraveny nerovnosti. Hotové díly jsou umístěny do meziskladu. Ohýbané prvky,
které vyžadují řádné vyschnutí, jsou upevněny do speciálních žebřů a uloženy
do meziskladu surových ohybů. Za jeden až dva týdny je dosažena požadovaná
vlhkost dřeva a tím i tvarová stálost.
V prvním poschodí výrobní haly jsou jednotlivé díly smontovány.
Kostra židle je ponořena do mořicí kádě, kde získá požadovaný odstín. Po
vysušení mohou být přidány čalouněné díly a další doplňky. Na konci montážní
dílny najdete kvalitářky, které vracejí nevyhovující výrobky k ručnímu
zapravení.
Za zákazníkem putují židle či stoly v kartonových krabících.
Pokud zákazník požaduje dodání v demontovaném stavu, je výrobek rozložen. Ze
skladu již míří výrobky za zákazníky.
ZDROJ: Moravské hospodářství
|